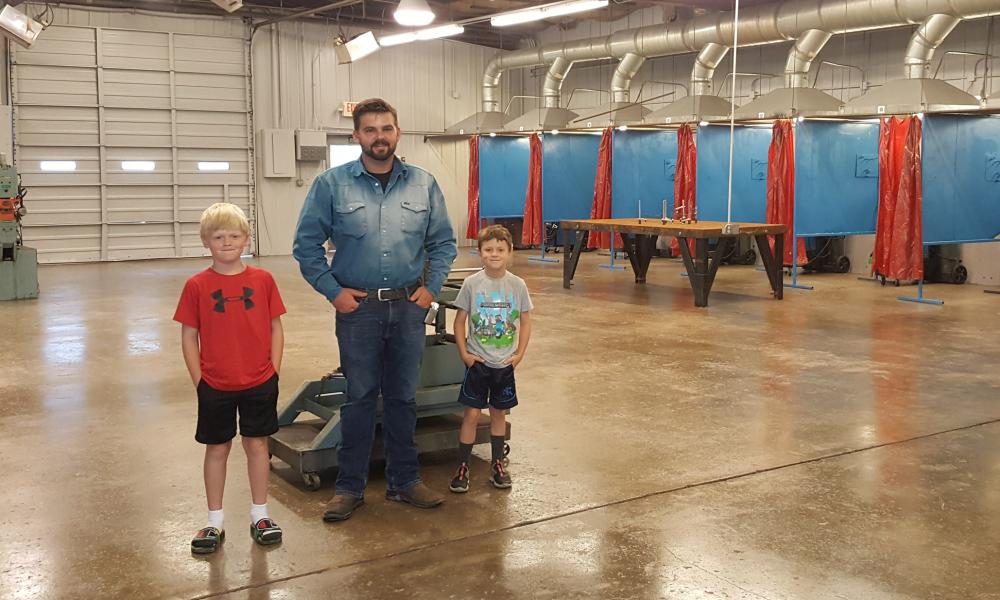
Olney Central College’s Welding Technology Building underwent renovations this summer that not only improved its aesthetics, but created more usable space for the program.
“This project has been a long time coming,” said Instructor Curtis Marshall. “Maverick (Fisher) came out over the summer and put a lot of time and effort into this. It has made for a cleaner shop and the logistics are much better.”
The building’s extensive overhaul included power washing and sealing the original cement floors, painting the walls and reorganizing workspaces.
“In all welding shops, you fight dust from grinding, which is super abrasive and hard on surfaces,” said Fisher, who serves as the Title III welding specialist. “It has been some time since the shop has undergone a complete cleaning. It’s been a two-month process, but the results are worth the effort.”
Along with cleaning the facility, Marshall created indoor access points for two storage areas, which run the length of the east and west sides of the lab. Previously, the area could only be entered through an outside door.
“Cutting the new doors created around 576 feet of usable, accessible space,” Fisher said. “We will be turning one area into a dedicated grinding room, which will help contain the dust and maintain the cleanliness of the lab.”
Marshall said reconfiguration of the lab also will increase student capacity.
“It’s going to give the students more room and a better work environment,” Marshall said. “Big projects will be easier to build and the facility will be safer than ever before for the students.”
The updates bring the on-campus facility in line with the new Title III Associate Degree Welding lab at the West Richland Center in Noble.
“I’ve been to several welding schools and I’ve seen their facilities,” Fisher said. “We now have the cleanest setup of any I’ve seen. With other associate degree programs, the first- and second-year students are all working in the same space. We have two facilities fully-dedicated to both groups.”
The new configuration also maximizes students’ hands-on experience.
“It’s more conducive to the program and means more welding time for the students,” Fisher said. “My outlook is students should walk away from our classes feeling every penny they spent was worth it. The meat and potatoes of our classes is the welding time and the changes will make it easier to achieve that goal.”
Marshall plans to make additional improvements to the classroom area in the future.
Later this fall, Shultz Electrical will be performing electrical upgrades, which will include installing new outlets and dropping extension cords from the ceiling for the welders.
Marshall and Fisher said the project would not have been possible without college and community help.
O&M Department’s Jerry Booker ensured needed tools were available while work study student Dylan Jones painted all welding booths and assisted with other jobs.
Student Ken Hake, who had previous experience sealing floors, aided Fisher with the process in the lab. Even Marshall’s sons, Jeremiah and Harrison, pitched in helping to squeegee the floors as needed.
Others involved included Wease Equipment, which provided the pressure washer, and Dirk Washburn of Color Your World, who painted the walls.